اشکالات تغذیه و توزیع مرکب
سیستم مرکبدان یک ماشین چاپ افست معمولاً شامل یک مرکبدان، نورد مرکب، نورد قطع و وصل تغذیه مرکب (نورد واسطه) سه یا چهار نورد آهنی صلایه، چهار نورد لاستیکی واسطه، سه یا چهار نورد روی زینک (نورد فرم) از جنس لاستیک و یا مواد مشابه دیگر است. نورد مرکب و نورد واسطه، کنترل تغذیه مقدار معینی از مرکب را به عهده دارند، نوردهای صلایه و نوردهای واسطه، یک لایه نازک از مرکب را به نوردهای روی زینک (نورد فرم) منتقل میکنند که این مرکب چاپ خواهد شد. نوردهای فرم (روی زینک) برحسب نیاز تصویر چاپی، مرکب را به قسمتهای چاپشونده منتقل میکنند.
برای کارکرد درست، حرکت نوردهای صلایه باید با دنده و یا زنجیره انجام شود. سرعت حرکت این نوردها باید با سرعت حرکت سیلندر زینک برابر باشد. حرکت نوردهای واسطه و نوردهای فرم فقط در اثر تماس سطح نوردها با یکدیگر انجام میشود.
حرکت نورد مرکب بهطور متناوب به وسیله شیطانک و یا کلاچ کنترل میشود، تنظیم تیغه مرکبدان و حرکت نورد مرکب تعیینکننده مقدار مرکبی است که به نوردهای دیگر منتقل شده و سرانجام بر روی کاغذ چاپ میشود.
توزیع یکنواخت مرکب بر روی نوردها در اثر حرکت نوردهای صلایه و متفاوت بودن قطر نوردها صورت میگیرد و قابل تنظیم است. ضخامت لایه مرکب از نظر توزیع آن در طول نورد، حتماً یک اندازه نیست. زیرا نیاز زینک به مرکب در قسمتهای مختلف آن ممکن است متفاوت باشد. با نصب و تنظیم یک تیغه مرکبدان لاستیکی در قسمتی خاص، میتوان نیاز به تغذیه مرکب در بخش مشخصی از سطح زینک را برآورده ساخت.
اشکالات معمول در سیستم مرکبدان به شرح ذیل است :
اشکال ۱ : خطها یا نوارهای افقی
خطهای ناخواسته روی نوردها همیشه موازی لب پنجه کاغذ هستند، برخلاف خطهای افقی که ناشی از خرابی دندههاست، خطهای افقی روی نوردها هیچ رابطهای با گام حرکت دندههای سیلندر ندارند.
خطهای افقی روی نوردها، ممکن است بهصورت یک خط و یا چند خط با فاصلهای متفاوت و یا مساوی با یکدیگر ظاهر شوند.
علت الف : ظاهر شدن خطها در اثر خرابی دندهها ( و اشکالات مربوط به برج چاپ شامل تنظیم سیلندرهای زینک ، لاستیک و کاغذ و نیز زیرسازی زینک و لاستیک که در فصل دوم شرح داده شد)
علت ب : یک یا چند نورد روی زینک به حالت سفت فیلر و تنظیم شده است.
نوردهای فرم با لبه زینک برخورد کرده و دچار نوسان میشوند. این عمل باعث گسیختگی مرکب از دو سر نورد شده و خطهای ناخواستهای را روی نورد ایجاد میکند. این خطها پس از یک دور چرخش نورد، بر روی زینک منتقل میشود. اگر قطر نوردهای فرم یکسان بوده و همگی نسبت به زینک، سفت فیلر شده باشند، پیدایش این خطها بیشتر خواهد بود. پیدایش خطها ناشی از خرابی دندهها اغلب در چاپ رنگ زمینه ترام بیشتر قابل دیدن است.
راهحل : فشار نوردهای فرم را نسبت به زینک و نوردهای صلایه تنظیم کنید.
علت ج : وجود لقی زیاد در سر نوردهای روی فرم باعث حرکت افقی آنها در ارتباط با نوردهای صلایه میشود. اگر در موقع حرکت معکوس نوردهای صلایه – نوردهای فرم بر روی زینک قرار داشته باشند، ممکن است سُرخوردگی در نوردها ایجاد شده و موجب پیدایش خطهای افقی شود.
راهحل ۱ : سر نوردها را تنظیم کنید تا لقی نوردها گرفته شود. در صورت لزوم میتوانید از واشر نیز استفاده کنید و با قرار دادن آن بر روی میل نورد، تنظیم لازم را انجام دهید.
راهحل ۲ : در بعضی از ماشینها میتوانید زمان چرخش معکوس نوردهای صلایه را به صورتی تنظیم کنید که نوردهای روی زینک در قسمت خالی از سیلندر قرار داشته باشند، اغلب باعث از بین رفتن خطهای ناشی از لقی سر نوردها میشود.
علت د : گیر کردن و سُرخوردن نوردها روی زینک.
اگر فشار نوردهای روی زینک با نوردهای صلایه و زینک نامساوی باشد، حالت گیر کردن نوردها پدید میآید، اگر فشار نوردها برابر نباشد، نورد در قسمتی که بهصورت سفتتر تنظیم شده گیر کرده و باعث پدید آمدن خط میشود. اگر سطح نوردها شیشهای شده باشد، امکان پدید آمدن این مشکل بیشتر خواهد بود.
راهحل ۱ : فشار نوردهای فرم را روی زینک کمتر از فشار آن نسبت به نوردهای صلایه تنظیم کنید.
راهحل ۲ : نوردهای فرم و نوردهای صلایه را به لاستیکسازی بدهید تا بریزند و حالت شیشهای آن از بین برود. براق شدن سطح نوردها بر اثر جمعشدن مرکب خشک شده و صمغ باقیمانده – که به وسیله مواد شستوشوکننده معمولی، کاملاً پاک نشدهاند – میباشد. برای رفع این مشکل از مواد پاککننده مخصوص استفاده کنید.
علت ه : لاستیک شل و لغزنده است.
چون کوتاه و بلند کردن طول چاپ (کار چاپی) اغلب مورد نیاز است. به همین دلیل سرعت حرکت سطح زینک و لاستیک همیشه با هم یکسان نیستند. اگر لاستیک شل باشد، توسط زینک به حرکت در میآید و ممکن است از روی سیلندر سُر بخورد، این سُرخوردگی باعث پیدایش خطهای ناخواسته میشود. اگر فشار بین سیلندر زینک و لاستیک را افزایش دهید، سُرخوردگی نیز افزایش پیدا میکند.
راهحل: لاستیک را سفت کنید، با استفاده از آمپر مخصوص، فشار بین زینک و لاستیک را اندازهگیری کنید. اگر فشار زیاد بود کاغذ زیر زینک و یا لاستیک را کم کنید.
علت و : خوردگی و خرابی تسمههای الکترو موتور اصلی.
اگر یکی از تسمهها ساییده شده و یا بیش از تسمههای دیگر سفت شده باشد، انتقال نیرو یکنواخت نخواهد بود، در نتیجه خطهای ناخواسته ظاهر میشوند.
راهحل: تسمههای موتور را تعویض کنید.
اشکالات لاستیک افست
اغلب لاستیکهای چاپ افست از چهار لایه کتان بافته شدهاند که با چسب لاستیکی مخصوص به یکدیگر چسبیده شده و سپس سطح آنها با ترکیبی از لاستیک، روکش شده است. ضخامت این روکش لاستیکی ۳/۰ تا ۵/۰ میلیمتر است و ضخامت کلی لاستیک در حدود ۵/۱ میلیمتر است. ضخامت لاستیک باید در سراسر سطح آن یکنواخت باشد. تغییرات ضخامت لاستیک نباید از ۰۱/۰ میلیمتر بیشتر باشد. در غیر این صورت کیفیت کار کاهش پیدا میکند. لاستیکهایی به صورت دو لایه، سه لایه و پنج لایه برای موارد خاص وجود دارد.
اغلب در ماشینهای افست ورقی لاستیک چهار لایه به صورت استاندارد عرضه میشود و با اضافه کردن کاغذ زیر لاستیک ارتفاع آن را به اندازه دلخواه در رابطه با آسوره سیلندر تنظیم میکنند. این ارتفاع توسط سازنده ماشین و بر حسب مشخصات و طول مورد نیاز چاپ محاسبه میشود. به منظور رویهم خوردن رنگها در چاپ چند رنگ به علت کش آمدن کاغذ در حین چاپ چند رنگ، تغییرات جزیی در زیرسازی لاستیک لازم است، اما اگر اضافه زیرسازی لاستیک با بیش از حدود ۱/۰ میلیمتر باشد، نتیجه آن لرزش تصویر و درشت شدن ترامها خواهد بود. در بعضی از ماشینهای افست اروپایی از دو لایه لاستیک استفاده شده است. این حالت میتواند تأثیر بهتری را در چاپ داشته باشد و قدرت چاپدهی را افزایش دهد.
لاستیکهای بادی در ساختمان خود محفظههای هوا دارند. به این ترتیب لاستیک، در موقع تماس با زینک قابلیت فشرده شدن و برگشت به شکل اولیه را دارد و بر عکس لاستیکهای معمولی که در موقع تماس با زینک برآمده شده و شکم میدهند، از کارآیی خوبی برخوردار است. لاستیک معمولی قابلیت جابجایی دارد ولی کاملاً به شکل اولیه خود برنمیگردد. ساختمان لاستیک بادی به شکلی است که آن را در مقابل فشار و تخریب مقاوم میکند، با وجود اینکه لاستیکهای بادی عملکرد بهتری نسبت به لاستیکهای معمولی دارند، فشار اضافی و زیربندی زیاد آن باعث درشت شدن ترامها میشود.
لاستیک به دور سیلندر بسته شده و تحت فشار مشخص قرار داده میشود تا از سرخوردن آن از روی سیلندر که در نتیجه فشار چاپ رخ میدهد، جلوگیری شود. از آنجاییکه بستن لاستیک با دست انجام میشود، میزان کردن کشش آن با دقت ممکن نیست. کشش لاستیک بهدور سیلندر، بین ۳۰ تا ۵۰ پوند در هر فوت متغیر است و این میزان به نوع لاستیک و ماشین چاپ بستگی دارد.
استفاده از آچار ترک ( دسته بکس مدرج به منظور تنظیم دقیق فشار ) برای سفت کردن و کشش یکنواخت لاستیک بسیار مهم است. بهخصوص در ماشینهای چاپ چند رنگ که تمام لاستیکها باید بهطور یکنواخت و با فشار مساوی بسته شوند. در بعضی از ماشینها نیاز به استفاده از آچار ترک مخصوص وجود دارد.
در موقع نصب لاستیک نو، فشار آن بهدور سیلندر و تأثیر کشیده شدن آن بهوسیله فشار چاپ، ممکن است باعث کشیدگی و شل شدن لاستیک شود، که در این صورت، در حین چاپ بایستی چند بار لاستیک را سفت کرد.
فشار ناشی از چاپ در چند هزار گردش اول، باعث کاهش ضخامت لاستیک نو میشود. اگر ضخامت لاستیک را با یک میکرومتر دقیق اندازهگیری کرده و مقدار زیر لاستیکی نیز بهصورتی به آن اضافه شود که به اندازه ۱/۰ میلیمتر، فشار چاپ را زیاد کند، ممکن است پس از چند صد برگ چاپ، متوجه کمبود فشار چاپ شوید. کنترل ارتفاع لاستیک به وسیله` میکرومتر مخصوص، ممکن است نشانگر این مطلب باشد که ضخامت لاستیک ۰۵/۰ میلیمتر کاهش داشته و نیاز به زیر لاستیکی اضافی برای دستیابی به چاپ بهتر وجود دارد.
در ابتدا روکش لاستیک از لاستیک طبیعی ساخته میشد، اما حالا این روکش از لاستیک مصنوعی است که چربی کمتری را جذب میکند و بنابراین مقاومت بیشتری را در مقابل برآمدگی و باد کردن و چسبندگی و شیشهای شدن نشان میدهد. چسبندگی سطح لاستیک همیشه به عنوان یک مشکل مطرح بوده است. کاهش قدرت جداسازی کاغذ از لاستیک را اغلب به عنوان یک مشکل شیمیایی و یا به علت ویژگی سطح لاستیک بررسی میکنند.
شیشهای شدن سطح لاستیک بهطور معمول به علت خشک شدن مرکب، صمغ، جذب چربی و دیگر مواد خشک کننده، در حین کار بهوجود میآید. این حالت اغلب باعث اکسید شدن سطح لاستیک و تخت شدن روکش لاستیکی، و کاهش قدرت ارتجاعی آن و در نتیجه کاهش قدرت دریافت مرکب توسط لاستیک میشود. مواد شیمیایی قوی نیز میتوانند لایه` پلاستیکی سطح لاستیک را از بین برده و آنرا سفت و سخت کنند. قدرت انتقال مرکب در یک لاستیک خشک و شیشهای شده، بسیار ضعیف است. ساییدن لاستیک با یک قطعه اسکاچ و پاک کردن آن با محلولهای مناسب میتواند کیفیت چاپ را تأمین کند.
بههر حال سطح لاستیک باید نرم، لطیف و پرزدار باشد. شستوشوی دقیق لاستیک میتواند از ایجاد بسیاری از مشکلات جلوگیری کند. اگر مواد پاککننده‡ لاستیک خیلی قوی باشند، باعث باد کردن لاستیک میشوند و اگر مواد شیمیایی مصرفی ضعیف باشند، توان پاک کردن مرکب و تمیز کردن کامل لاستیک را نخواهند داشت. فروشندگان مواد شیمیایی چاپ، مواد پاک کننده مخصوصی را عرضه میکنند که ضمن پاک کردن مؤثر مرکب از روی لاستیک و نورد، از باد کردن آن نیز جلوگیری میکند.
اشکالات اساسی لاستیک افست به شرح ذیل است :
اشکال اول – شفافیت و روشنی تصویر به تدریج از بین میرود.
علت الف : لاستیک تحت فشار قرار دارد. از دست رفتن چاپ به علت نازک شدن لاستیک تحت فشار گردش سیلندر اتفاق میافتد.
راهحل : با استفاده از میکرومتر مخصوص، ارتفاع زیربندی لاستیک را نسبت به زینک کنترل و اندازهگیری کنید. اگر ارتفاع لاستیک کاهش پیدا کرده باشد، کاغذ زیر لاستیکی با ضخامت مناسب را به زیربندی لاستیک اضافه کنید، اگر ارتفاع لاستیک تغییر پیدا نکرده باشد، علت مشکل ممکن است در خرابی زینک باشد.
علت ب : افزایش فشار چاپ که به علت باد کردن و برجسته شدن لاستیک پدید آمده باشد. این شرایط ممکن است به علت عدم مقاومت کافی لاستیک در مقابل چربی و مواد شیمیایی بوده و یا به علت شستوشوی نامناسب لاستیک باشد.
راهحل ۱ : ارتفاع لاستیک را با استفاده از ابزار اندازهگیری کنترل کنید، اگر ارتفاع لاستیک افزایش پیدا کرده بود، کاغذ زیرلاستیکی را کاهش دهید. اگر با این کارها چاپ اصلاح نشد، ضعیف شدن زینک و از دست دادن قدرت جذب مرکب را بوسیله زینک کنترل کنید.(به مطالب قبلی درباره مسایل زینک و چاپ رجوع کنید.)
راهحل ۲ : لاستیک را با دقت بشویید.
علت ج : استفاده از مرکبهای هیت ست ( Heat set) مرکبی که بوسیله حرارت خشک میشود و یا مرکبهای کوئیکست (Quick set) مرکبی که خیلی سریع خشک میشود با لاستیک معمولی. این حالت باعث ایجاد فشار اضافی و برجسته شدن قسمتهای چاپ شونده بر روی لاستیک میشود.
راهحل : لاستیک را تعویض کرده و از نوعی که برای کار با مرکب هیتست و یا کوئیکست طراحی شده است استفاده کنید.
علت د : از دست دادن قدرت مرکبگیری لاستیک به علت سخت و شیشهای شدن لاستیک. این حالت در نتیجه خشک شدن چربی، صمغ و مواد خشک کننده دیگر، بر روی لاستیک بهوجود میآید.
راهحل : لاستیک را با مواد پاککننده و آب شستوشو دهید، سپس با اسکاچ و محلول پاککننده تمیز کنید تا حالت شیشهای آن از بین برود.
توجه: لاستیک باید بهطور کامل تمیز شده و هیچ نوع جسم خارجی روی آن باقی نمانده باشد، استفاده از مواد پاک کننده با کیفیت خوب ضروری است. این نوع شستوشو راه بسیار سادهای برای جلوگیری از بسیاری مشکلات مربوط به لاستیک است.
اشکال دوم- سایه (اثر) تصویر بهجا مانده از کار قبلی بر روی لاستیک.
علت : باد کردن لاستیک در اثر جذب حامل مرکب حین چاپ قبلی.
راهحل ۱ : لاستیک را تعویض کنید.
توجه: لاستیک قدیمی را بهطور کامل تمیز کرده و با پولیش لاستیک آغشته کنید، سپس آن را در محل تاریک آویزان کنید. این روش باعث دفع چربی از لاستیک شده و احتمال باد کردن آن را کم میکند.
راهحل ۲ : در مورد مواد تشکیلدهنده مرکب با فروشنده آن مشورت کنید.
اشکال سوم- کاغذ به قسمتهای بدون چاپ لاستیک میچسبد.
علت : چسبندگی لاستیک به علت استفاده از مواد شیمیایی قوی و یا اکسید شدن و جذب و خشک شدن چربی در آن. این حالت به دلیل استفاده از خشککنهای محتوی منگنز و یا لاجورد پدید میآید. در لاستیکهای جدید که از مواد مصنوعی ساخته شدهاند، وجود این مشکل غیر عادی است.
راهحل ۱ : از لاستیک سیلندر با قدرت رهاسازی (ول کردن) بیشتر استفاده کنید.
راهحل ۲ : از لاک و یا مواد سخت کننده دیگر، برای جلوگیری از چسبندگی لاستیک استفاده کنید. البته این روش بسیار موقتی بوده و در نهایت لاستیک را باید باز کرده و بهطور کامل شستوشو دهید تا حالت چسبندگی آن از بین برود. سپس لاستیک را با اسکاچ و محلول پاک کننده بسایید تا سطح شیشهای آن بهطور کامل پاک شده و لاستیک دوباره پرزدار شود.
اشکال چهارم- یکنواخت نبودن چاپ.
علت الف : ضخامت لاستیک یکنواخت نیست. (به مطالب قبلی مربوط به یونیت چاپ و اشکال یکدست نبودن رنگ توجه کنید.)
راهحل : لاستیک را تعویض کنید، از لاستیک با کیفیت خوب استفاده کنید و دقت داشته باشید که در موقع خرید، لاستیک در شرایط خوبی قرار داشته باشد.
علت ب : خوردگی سطح سیلندرها. (به مطالب قبلی مربوط به یونیت چاپ و اشکال یکدست نبودن رنگ مراجعه کنید.)
علت ج : صاف نبودن سیلندر و یا وجود بار اضافی بر روی آسوره سیلندر.
راهحل : سیلندر را کنترل کنید.
اشکال پنجم- پارگی، دندانه دار شدن و یا جا خوردن (له شدن) لاستیک.
علت : عبور جسم خارجی، لایی کاغذ یا پوشال، کاغذ تا شده، بهخصوص کاغذهای ضخیم و مقوا از داخل ماشین.
راهحل ۱ : اگر سطح لاستیک دچار پارگی شده است آنرا تعویض کنید. با استفاده از مواد مصرفی نامرغوب، چاپ با کیفیت خوب انجام نخواهد شد.
راهحل ۲ : اگر سطح لاستیک پارگی نداشته ولی کنگره دار و یا جاخورده شده باشد، قسمتهای آسیب دیده را بشویید بلکه ور بیاید (باد کند). سپس با استفاده از کاغذهای بریده شده به اندازه مناطق جاخورده و قرار دادن آن در زیر قسمتهای فرو رفته، لاستیک را به ارتفاع معمول برسانید.
اشکال ششم- وجود خطوط و نوارهای افقی در چاپ.
علت : لاستیک شل و یازیر لاستیکی آن زیاد است.
راهحل : لاستیک را سفت کنید، با استفاده از میکرومتر مخصوص، زیربندی زینک و لاستیک و فشار آنرا کنترل کنید و کاغذ زیر زینک و لاستیک را چنانچه اضافه است، خارج سازید.
اشکال هفتم- لرزش تصویر.
علت الف : لاستیک شل است
راهحل : لاستیک را بهطور یکنواخت سفت کنید.
علت ب : گیره لاستیک با دقت بسته نشده و یا به آن چسبیده است.
راهحل ۱ : لاستیک را با دقت در گیره قرار دهید.
راهحل ۲ : از لاستیک نو استفاده کنید.
علت ج : زیر لاستیکی نامناسب است.
راهحل : از زیر لاستیکی مرغوب استفاده کنید، حداکثر دو برگ زیرلاستیکی بهکار ببرید.
اشکال هشتم- نقص در رویهم خوردن رنگها.
علت الف : لاستیک شل شده است.
راهحل : لاستیک را سفت کنید.
علت ب : چسبندگی و یا شیشهای شدن سطح لاستیک که موجب جداسازی کاغذ از سطح لاستیک با نیروی غیر یکنواخت میشود.
راهحل : لاستیک را ترمیم و یا تعویض کنید.
تغذیه مرکب یکنواخت نیست
تنظیم نوردها به روش نواری
با چرخش متناوب نورد، مرکب به نوردها میرسد. کنترل تغذیه مرکب با تنظیم تیغه مرکبدان صورت میگیرد که به وسیله آن مقدار مرکب لازم برحسب نیاز کار چاپی به قسمتهای مختلف زینک انتقال پیدا میکند. نوسان و چرخش نورد، مرکب لازم را به تمام سطح زینک میرساند. نورد رابط تبادلکننده تماس بین غلتک مرکبدان و نورد صلایه بالایی است. این نورد، نواری از مرکب تازه را به نورد صلایه منتقل میکند. این نوار تا رسیدن به نوردهای روی زینک نازک شده و بهصورت لایه نازکی از مرکب در خواهد آمد. حرکت جانبی نوردهای صلایه موجب پخش شدن یکنواخت مرکب در سرتاسر طول چاپ میشود. حرکت جانبی نوردها قابل تنظیم است تا مقدارمرکب لازم به تمام مناطق منتقل شود. اگر با دو یا سه رنگ بهطور تفکیک شده از مرکبدان کار شود، حرکت جانبی نوردها به حداقل کاهش مییابد.
علت الف : خط دار شدن نوردهای مرکب
این حالت در نتیجه شیشهای شدن نوردها رخ میدهد، شیشهای شدن به علت تغذیه آب زیاد و نیز صمغ یا اسید فسفریک اضافی و یا هر دوی آنها در محلول آب اتفاق میافتد. وجود رطوبت زیاد باعث اشباع شدن نوردها شده و کار انتقال مرکب را با اشکال روبهرو میکند، در نتیجه ثبات رنگ از بین خواهد رفت. اغلب نوردهای صلایه فلزی در این موقع دچار اشکال میشوند، ولی اگر سطح نوردهای لاستیکی نیز شیشهای شده باشد، حالت خطدار شدن مرکب در آن نیز ظاهر میشود.
راهحل ۱ : نوردها را با روش دو مرحلهای (یا سه مرحلهای) شستشو دهید.
راهحل ۲ : اگر خطدار شدن مرکب فقط در نوردهای صلایه فلزی رخ داده باشد، سیستم مرکبدان را شستشو داده، نوردهای روی زینک و نوردهای واسطه را خارج کرده و نوردهای صلایه فلزی را کاملاً تمیز کنید.
راهحل ۳ : اگر بریدگی و خطدار شدن مرکب در نوردهای لاستیکی باشد، قسمتهای شیشهای شده نورد را پاک کنید. (توجه: در موقع شستشوی نوردها از دستکش و روپوش پلاستیکی استفاده کنید) سنگ زدن نوردها، راه دیگر رفع شیشهای شدن نوردهاست.
راهحل ۴ : از آنجایی که علت اصلی بریدگی مرکب وجود نوردهای صلایه فلزی است، میتوانید این نوردها را با لوله پولیکا روکش کنید که مقاومت زیادی در برابر بریدگی مرکب نشان میدهد.
علت ب : مرکب از روی نورد مرکبدان برگشت کرده، در نتیجه تغذیه مرکب کاهش پیدا میکند.
در حقیقت، مرکب از روی نورد برگشت نمیکند، بلکه روی نورد باقیمانده و جریان پیدا نمیکند. این نوع مرکب ممکن است خیلی سرد بوده و به راحتی جریان پیدا نکند و یا بیش از اندازه رقیق باشد.
راهحل ۱ : گاه به گاه مرکب را در در مرکبدان با کاردک هم بزنید تا به راحتی جریان پیدا کند.
راهحل ۲ : از همزن مکانیکی در سینی مرکبدان استفاده کنید.
راهحل ۳ : از مرکب شلتر یا مرکبی که به راحتی جریان پیدا میکند، استفاده کنید.
راهحل ۴ : درجه حرارت محیط ماشین خانه را افزایش دهید. اکثر مرکبهای چاپ در درجه حرارت ۲۱ الی ۲۴ درجه سانتیگراد بهترین کارآیی را دارند.
علت ج : جمع شدن مرکب بر روی نوردها و قسمتهای چاپشونده زینک و لاستیک.
در این شرایط مرکب بهطور کامل انتقال پیدا نکرده و در نتیجه تصویر کمرنگ میشود. جمع شدن مرکب ممکن است در اثر پراکندگی رنگدانه (پیگمنت) و یا پرآب شدن آن باشد
( و همچنین زیرسازی و فشار بین سیلندرهای لاستیک و زینک موجب بروز این مشکل هستند.)
راهحل ۱ : درجه پراکندگی رنگدانه مرکب را به وسیله ابزار اندازهگیری ریزدانه بودن مرکب کنترل کنید. اگر مرکب زبر بود، باید دوباره آسیاب شود. این کار معمولاً در چاپخانهها عملی نیست و بایستی در این مورد از کارخانه سازنده مرکب کمک گرفت.
راهحل ۲ : رطوبت زینک را به حداقل کاهش دهید، اگر این کارها مؤثر نبود، مقدار کمی ورنی مقاوم به آب را به مرکب اضافه کنید و یا از مرکبی که نسبت به آن مقاوم است استفاده کنید.
علت د : نوردهای روی زینک و یا لاستیک سیلندر، در اثر پرز کاغذ کثیف شدهاند.
پرز کاغذ از مواد سلولزی است که در اثر جذب آب حالت دفعکننده مرکب را پیدا کرده و در نتیجه مانع از جریان یافتن و انتقال یکنواخت مرکب میشود.
راهحل ۱ : نوردها را با نوردشوی تمیز کنید، نوردها را با دست تمیز کنید.
راهحل ۲ : چسبندگی مرکب را کم کنید.
راهحل ۳ : از کاغذ کمپرز استفاده کنید.
راهحل ۴ : از دستگاه پرزگیر کاغذ استفاده کنید.
علت ه : خوردگی و گودی روی نوردها، مانع از تماس یکنواخت بین آنها و نوردهای روی زینک میشود.
راهحل ۱ : نورد خراب را تعویض کنید.
راهحل ۲ : نوردهای خراب را بیرون بیاورید و سنگ بزنید.
علت و : خمیدگی میل نورد.
راهحل : نوردهای خراب را باز کرده، میل نورد را تعمیر کرده و بار دیگر نورد را روکش کنید.
علت ز : خمیدگی تیغه مرکبدان و خوردگی لاستیک آن، این شرایط مانع از تنظیم دقیق تیغه مرکبدان میشود.
راهحل : از تیغه مرکبدان نو و صاف استفاده کنید. در موقع نصب دقت کنید. پیچهای مرکبدان کاملاً باز بوده و به حالت آزاد قرار داشته باشند، تیغه مرکبدان را طبق دستور کار ماشین با استفاده از فیلر تنظیم کنید، فاصله تیغه مرکبدان بهطور معمول ۳/۰ تا ۵/۰ میلیمتر است. در حالی که تیغه مرکبدان موازی با نورد مرکب باشد، تنظیمات بعدی را براساس نیاز کار چاپی انجام دهید، هرگز تیغه مرکبدان را با فشار روی نورد قرار ندهید، چنین شرایطی باعث خوردگی و ناصافی تیغه خواهد شد برای بستن تیغه مرکبدان ابتدا پیچهای وسطی را سفت کرده و سپس پیچهای کناری را ببندید. در زمان باز کردن تیغه ابتدا از دو انتهای آن شروع کرده و سپس به طرف وسط ادامه دهید.
علت ح : جمع شدن آشغال و یا مرکب خشک شده بین تیغه مرکبدان و نورد و مخلوط شدن آنها با مرکب دریافت شده از مرکبدان.
راهحل : تیغه مرکبدان و نورد را همیشه تمیز نگهدارید.
علت ط : مرکب خشک شده و مواد شیمیایی باقیمانده در دو سر نورد که در اثر استفاده از مایع نوردشوی به وجود آمده است و باعث باد کردن و یا پوسته شدن لاستیک نورد میشود. نتیجه این حالت ضعیف شدن قدرت مرکبدهی در کنارههای زینک است.
راهحل : پس از خاتمه کار نوردشویی، همیشه دو سر انتهایی نورد را پاک کرده و کاملاً خشک کنید. نوردهای آسیبدیده را تعویض کنید.
لک شدن کاغذ چاپ شده
علت الف : لکههای مرکب (بر روی سطح چاپ شده) وقتی ظاهرمیشوند که تصویر خشک نشده مرکبی، با سیلندر رابط تماس پیدا میکند، در ماشینهای چاپ چند رنگ، کاغذ چاپ شده اغلب پس از جدا شدن از سیلندر لاستیک، بلافاصله به وسیله سیلندر رابط حمل و منتقل میشود.
راهحل ۱ : برای رفع این اشکال میتوانید از محافظ کاغذ بر روی سیلندر رابط استفادهکنید. این پوشش محافظ با نام تجاری سوپر بلو (Supper Blue) شناخته شده است.
راهحل ۲ : یشتر ماشینهای چاپ، سیلندر رابط را با طلق شیشهای ناصاف و یا مواد دیگری که از سرخوردن کاغذ جلوگیری میکند میپوشانند، در این مورد باید با دقت کافی عمل شود. در ماشینهایی که برای انتقال کاغذ از قرقره و یا ستارههای کائوچویی بر روی سیلندر رابط استفاده شده باشد، باید دقت شود فرمبندی به صورتی باشد که فضای خالی برای حرکت این قرقرهها وجود داشته باشد، در جایی که این نکته رعایت نشده باشد، استفاده از نخ یا سیم که بین دو قرقره کشیده شده باشد، مؤثر خواهد بود.
علت ب : کاغذ در حالتی که تحت فشار چاپ قراردارد (در نقطه تماس بین دو سیلندر) چروک میشود. یا تماس کاغذ با سیلندر چاپ در بعضی نقاط زودرس و نابهنگام است. این چینخوردگی و چروک، در صورت ناصاف بودن کاغذ اتفاق میافتد و تصویر چاپ شده بر روی آن به شکل کمرنگ و دوبله و در مجاورت تصویر اصلی ظاهرمیشود. چنین علایمی اغلب در سطح کاغذ پراکنده نخواهد بود و فقط در فضاهای معینی از چاپ اتفاق میافتد.
راهحل ۱ : تغذیه کاغذ تخته جلو را کنترل کنید. (زمان تغذیه کاغذ، تنظیم نشان، ارتفاع فوتک(
راهحل ۲ : کاغذ را عوض کنید.
راهحل ۳ : مویی نگهدارنده کاغذ را روی سیلندر چاپ نصبکنید، این روش فقط در ماشینهای چاپ تک رنگ و برج اول چاپ در ماشینهای چند رنگ انجاممیشود. در برجهای چاپ بعدی در ماشینهای چند رنگ، ممکن است میلههای باد و یا وسایل نگهدارنده الکتریکی لازم باشد.
راهحل ۴ : برای صافکردن لبه کاغذ آن را در رطوبت مناسب قرارداده و شرایط صاف شدن لبههای کاغذ را فراهم سازید.
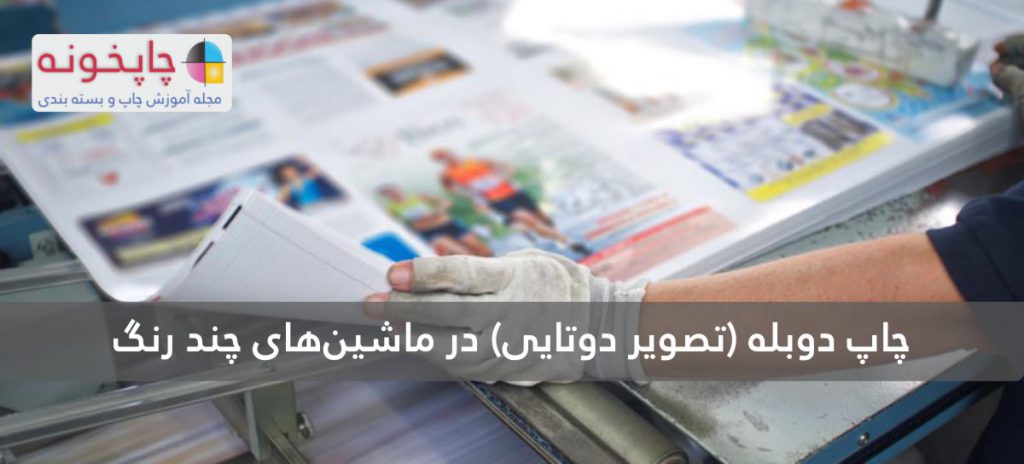
چاپ دوبله (تصویر دوتایی) در ماشینهای چند رنگ
چاپدوبله یکی از موارد خاص و نشاندهنده تنظیم نبودن ماشین است. در ماشینهای چندرنگ، تصویر چاپ شده روی یک برگ کاغذ، پس از عبور از برج اول، به لاستیک برج بعدی منتقل میشود، این تصویر ناخواسته بر روی برگ بعدی چاپ میشود، اگر این تصویر به دقت با چاپ اصلی منطبق نباشد، حالت چاپدوبله نمایان میشود.
چاپدوبله بهخصوص در چاپ ترامه خودنمایی میکند، چون در هر برگ از چاپ، تفاوت دیده میشود و موجب تغییر رنگ در تصویر خواهد شد.
علت الف : سرخوردن کاغذ از بین پنجهها. اگر لبه کاغذ از بین پنجهها خارجشود، در چاپ بعدی رنگها رویهمنمیخورند که باعث چاپ دوبله و افزایش قدرت رنگ میشود. چون سرخوردن کاغذها از بین پنجهها یکسان نیست، بنابراین رنگهای چاپ شده در هر برگ با برگهای دیگر متفاوت خواهد بود.
راهحل ۱ : دقت کنید که پنجهها تمیز بوده و بهطور صحیح عملکنند.
راهحل ۲ : پنجههای سیلندر چاپ و رابط را تنظیم کرده، و دقتکنید که پنجهها از کشش کافی و یکنواخت برخوردار باشند.
راهحل ۳ : لقی میل پنجهها و خوردگی بوشهای سر میل و فشار فنر را کنترل کنید، هرگونه اشکالی از این قبیل باید اصلاح و برطرف شود.
راهحل ۴ : قرقره روی لنگ پنجهها را کنترل کنید. سطح قرقره پنجهها باید صاف و بدون هیچگونه لقی عملکند. در بعضی از قرقرهها مقدار کمی لقی جانبی، قابل چشمپوشی است.
راهحل ۵ : لنگها را کنترلکنید، لبههای لنگ نباید تیز و یا دندانهدار شده باشد، اگر این طور بود آنها را تعویضکنید.
راهحل ۶ : چسبندگی مرکب را در برج چاپی که سر خوردگی کاغذ در آن اتفاق میافتد، کم کنید. بهتر است از این برج چاپ برای چاپ قسمتهای تنپلات استفادهکنید.
علت ب : لقی سرسیلندرهای چاپ و رابط، لقی دو طرف سیلندر، پیچیدگی سرسیلندرها و بوشها، و یا بلبرینگهای سرسیلندر.
راهحل : ماشین را تعمیر اساسی کرده، قطعات فرسوده را تعویضکنید.
علت ج : اشکال مکانیکی، چاپ دوبله با منشاء اشکال مکانیکی به غیر از سّرخوردن کاغذ از بین پنجهها، اغلب بهطور تکراری و با ترتیب خاص (مثلاً در هر دو یا سه برگ در میان اتفاق میافتد)
راهحل : در این مورد باید با متخصص فنی مشورت شود، عملکرد ماشین باید کنترل شده و قسمتی که باعث چاپ دوبله میشود، شناسایی شود. قسمتهای مورد بررسی میتوانند، پنجههای سیلندر رابط – در ماشینهایی که مجهز به دو یا سه سری پنجه رابط هستند – و یا سیستم آب، حرکت اجزای سیستم تغذیه مرکب و حرکت جانبی نوردهای صلایه باشد. در صورت امکان میتوانید هر یک از نوردهای صلایه را متوقفکرده و تغییر حالت احتمالی در چاپ دوبله را مشاهده کنید، سپس هر یک از قسمتهای آسیبدیده را تعمیرکنید. اگر اشکال مربوطه در یک سری از پنجههای رابط باشد، یک تکه؟ کوچک نمدار بر روی سکوی پنجه سیلندر رابط بچسبانید و آن را کمی مرکبیکنید، به صورتی که کاغذها در موقع عبور علامتگذاری شوند، حداقل ۳۰ برگ را به این صورت چاپ کنید، سپس نسبت چاپ دوبله را در برگهای علامتگذاری شده کنترلکنید، با این روش میتوان منبع اشکال را شناسایی کرد، که در نهایت تعمیر و یا تعویض آن ضروری است.
علت د : موجدار شدن و تغییر فرم لبه کاغذ در جریان چاپ.
متأسفانه تغییر فرم برگهای چاپ شده مشابه یکدیگر نیست. به عبارت دیگر تغییر شکل دو برگ کاغذ که در یک برج چاپ شده باشند، مشابه یکدیگر نیست، در نتیجه چاپ رنگ آخر میتواند موجب تغییر حالت تصویر بر روی لاستیک گردد که موجب چاپ دوبله و تغییر رنگ میشود.
راهحل ۱ : لفاف بندهای کاغذ یا پالت مقوا را تا موقع استفاده از آن باز کنید، در موقع نگهداری در انبار آن را لفافپیچ کنید.
راهحل ۲ : کاغذهای چاپ شده را با لفاف پلاستیکی بپوشانید.
راهحل ۳ : رطوبت محیط ماشین خانه را کنترل کنید.
راهحل ۴ : کاغذ را تعویض کنید.
علت ه : استفاده از کاغذ رول باز شده از چند رول متفاوت. در اغلب موارد دوبله شدن چاپ ممکن است به علت استفاده از کاغذهایی باشد که از چند رول مختلف، با ویژگیهای متفاوت باز و برش شده باشند.
راهحل : ۱۵ تا ۲۰ برگ کاغذ مشابه و با مارک متفاوت از کاغذهای مصرفی خود را چاپ کرده و تغییر حالت دوبله شدن را مورد کنترل و بررسی قرار دهید.